Forklift battery safety is a critical concern in industrial environments, and adhering to the guidelines set forth by OSHA (Occupational Safety and Health Administration) is essential for maintaining a secure workplace. Proper forklift battery handling, as highlighted by OSHA’s Severe Injury Reports—mandatory for employers to file since January 1, 2015—plays a significant role in reducing workplace accidents. These reports have recorded 60,912 entries as of August 2021, with a small fraction, less than 1% (52 incidents), relating to injuries from handling batteries for electric forklifts, pallet jacks, and electric vehicles.
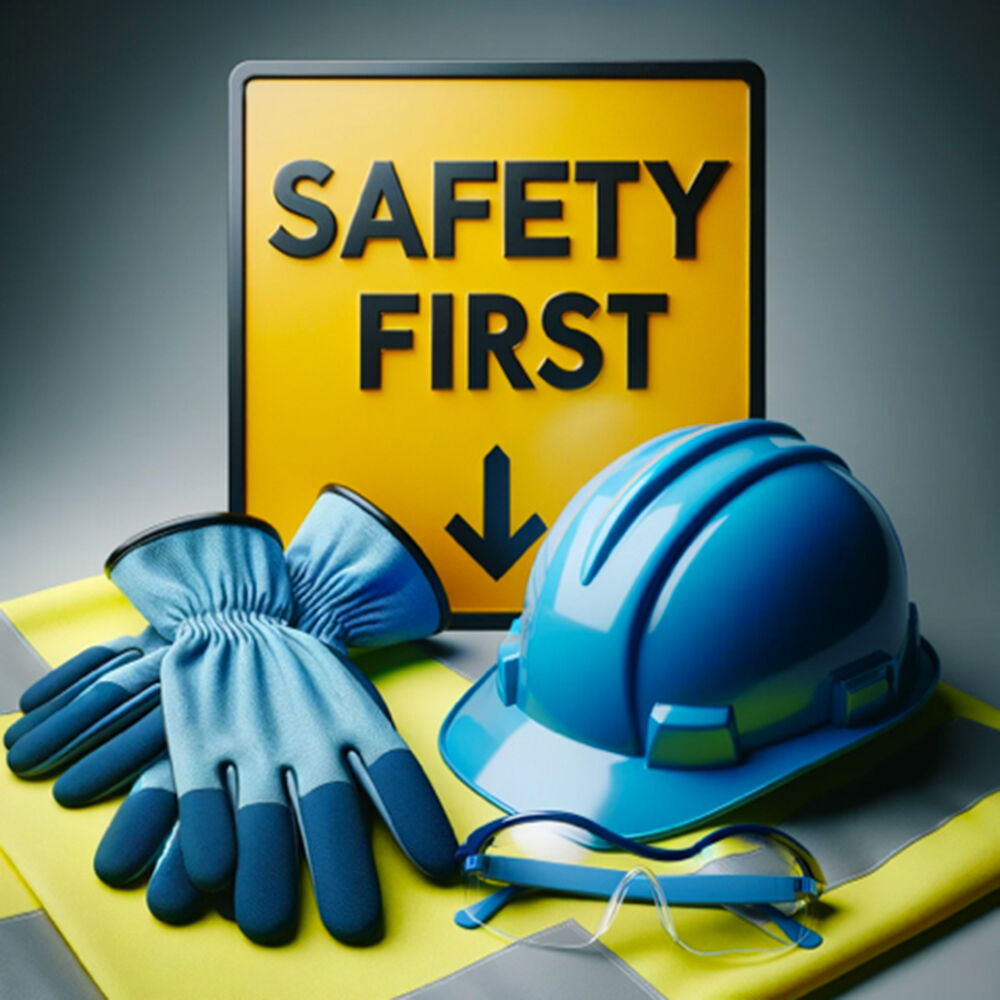
OSHA data says that most battery-related incidents occur during battery moving or watering
Fifty-two people suffered severe injuries, which could have been avoided. When were workers hurt?
To enhance forklift battery safety, it’s crucial to understand the risks involved in battery replacement, relocation, and maintenance—processes that have historically led to injuries like fractures, compressions, and acid burns. These incidents underscore the dangers associated with the substantial weight, large dimensions, and chemical hazards of traditional lead-acid batteries.
For material handling operations that use only one battery per lift truck, there is no need to switch batteries or perform maintenance daily. In fact, it’s often more cost-effective to switch to lithium batteries for your forklift fleet. This change will significantly reduce the safety risks associated with lead-acid batteries.
Why aren’t lithium batteries featured in OSHA injury logs?
The explanation is clear-cut: the reputable lithium forklift batteries available in the US adhere to stringent safety protocols, effectively avoiding incidents in OSHA data. These batteries are designed to meet Underwriters Laboratories (UL) guidelines thoroughly.
Underwriters Laboratories (UL), a global safety certification organization with a presence in over 100 countries and a century-long history, is recognized by OSHA among the Nationally Recognized Testing Laboratories (NRTL). UL, at the forefront of safety science, conducts comprehensive testing for numerous products, including industrial batteries, across various sectors. UL’s safety criteria ensure exceptional industrial practices, as outlined in UL’s battery testing procedures.
Two specific UL certifications pertain to lithium-ion batteries:
UL 2580, assessing batteries for electric vehicles, focuses on the safety of the energy storage assembly under simulated abuse conditions, safeguarding against any potential harm. The standard encompasses a series of mechanical and electrical tests, including overcharge, short-circuit, and thermal-stability assessments.
UL 991 evaluates safety-related controls utilizing solid-state devices, particularly the Battery Management System (BMS). This set of tests complements battery standards, targeting the electronic aspects of battery controls to mitigate fire, electric shock, or injury risks.
These rigorous tests solidify lithium batteries’ safety status. Lithium forklift batteries enable a “single-battery” operational model, eliminating the need for frequent battery swapping and other hazards associated with lead-acid batteries.
The top lithium providers such as Electrovaya, Flux Power, Green Cubes, and OneCharge Lithium Batteries, leverage cutting-edge technology to meet and often exceed UL and OSHA standards.
Lithium Iron (Ferrum) Phosphate (LFP) cells are lauded as the safest and most reliable in the US, due to their higher thermal stability and longevity. LFP technology’s advantages over NMC and other chemistries are detailed in comparative degradation tests.
OneCharge exemplifies an LFP industrial battery equipped with an advanced, dependable BMS featuring data logging and IoT integration, enhancing operational safety. With multiple safety layers, OneCharge batteries prevent overheating and malfunctions, with automated shutdowns to counter potential threats.
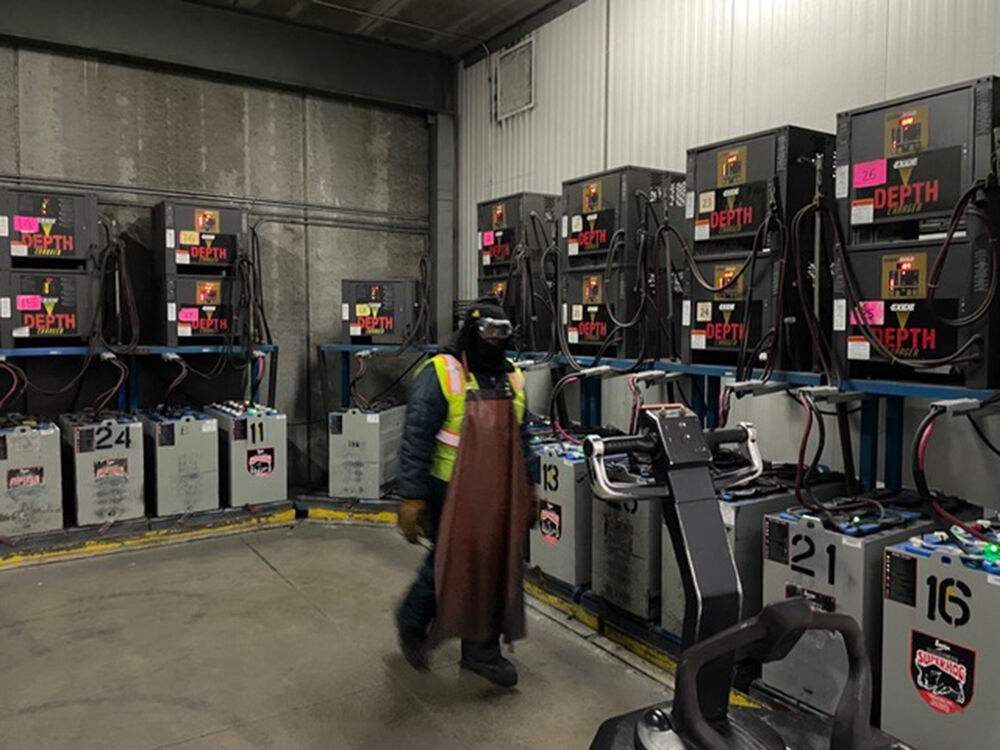
The lithium segment is growing fast
Lithium technology is revolutionizing the forklift industry, phasing out lead-acid batteries in favor of more dependable and safe lithium options with a better ROI. Predictions suggest lithium batteries will dominate half of the industrial battery market by 2032, with growth set to surge due to significant investments in lithium cell production and recycling, alongside declining raw material costs.